Tin Whisker Mitigation
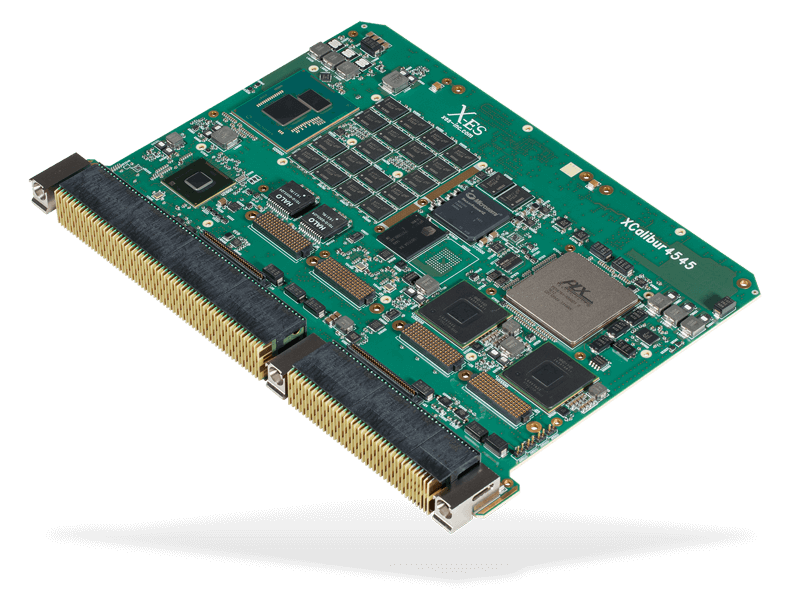
Tin Whisker Mitigation
In the past twenty years, continued reports of system failures due to tin whiskers have renewed interest in a once-obscure problem. At X-ES, we know that subtle aspects of material selection and system design can be mission-critical for high-reliability applications.
Our engineers have expertise in a variety of tin whisker mitigation techniques and can implement strategies tailored to the needs of any program.
A Tiny Filament Can Cause Big Damage
Tin whiskers are hair-like crystalline filaments that grow outward from the surfaces of certain metals, including tin. Although they can grow on other metals, they’re called “tin whiskers” because the widespread use of tin plating and solder has made them a cause for concern in some segments of the electronics industry.
Tin whiskers are typically less than 1 mm in length and can grow to lengths of up to 10 mm. They conduct electricity and can cause short circuits if they grow long enough to connect adjacent circuit elements.
Tin whiskers have been reported as the cause of electronic system failures in satellites, weapons systems, and medical devices, to name a few. In some cases, these failures resulted in product recalls, destruction of equipment, or complete loss of mission.
Unknown Cause, Multiple Approaches
The mechanism of tin whisker formation has not been established. While most researchers agree that whiskers form in response to compressive stress in the tin film, that stress could come from many different sources.
With no clear consensus on what causes whiskers, a number of techniques have been proposed to contain, prevent, or slow their growth, with varying degrees of success. Standard techniques are documented in GEIA-STD-0005-2: Standard for Mitigating the Effects of Tin Whiskers in Aerospace and High Performance Electronic Systems.
All Options on the Table
X-ES has experience with the full range of industry-standard tin whisker mitigation techniques, including both leaded and lead-free approaches. Our engineers craft mitigation strategies on a case-by-case basis, working closely with customers to identify the techniques best suited to program requirements. These strategies often fall into one of three tiers, based on the customer’s risk tolerance.
For programs that require verification of elemental composition, our engineers can also perform on-site x-ray fluorescence (XRF) analysis of all components.
Tier 1: Lowest Risk
Minimize the risk of failure due to tin whiskers to the fullest extent possible.
Do one or both of the following:
- Select components with leaded plating or refinish components to add leaded plating. Use a leaded solder process.
- Apply a hard conformal coating to components, parts of the board, or the entire board. For example, polyurethane coatings have been shown to contain tin whiskers for up to 11 years.
Tier 2: Moderate Risk
Some risk of failure due to tin whiskers is acceptable.
Use one or more techniques that show some evidence of reducing the risk of short circuits, such as:
- Applying a soft conformal coating.
- Avoiding fine-pitch components of pure tin.
- Avoiding bright tin.
- Using components with annealed plating.
Tier 3: Highest Risk
Take no steps to mitigate the risk of failure due to tin whiskers. Accept consumer-grade reliability and product life.